Everything You Need To Know About QFD
Create a QFD Diagram Online Free Free Download Free Download Free Download Free DownloadWhat Is QFD?
Today the average consumer seems to have a plethora of choices to decide from for similar goods, products and services. Many people decide according to a general perception of quality or worth. While working on determining what you need to do to please your consumers or even attract them, the implementation of quality function deployment is an essential element. Thus, organizations are suggested to use a structured framework to identify the needs and desires of their clients and develop them into detailed product specifications and production processes to deliver products that fulfil the needs of the consumer. The method or device they use is called Quality Function Deployment (QFD).
Quality function deployment is abbreviated as QFD. The definition of QFD is a framework designed to convert and implement the VoC into the quality characteristics of products, procedures and facilities to improve customer satisfaction.” The phrase ‘voice of the consumer (VOC)’ is used to define both stated and unstated customer needs or expectations.
After information regarding customer expectations has been acquired, techniques such as quality function deployment can be vital in linking the customer's voice to internal procedures. QFD is not just a quality improvement method but an essential resource for planning. In addition, QFD is also a service and product design framework focused upon consumer expectations, a structure that transitions from customer requirements to product or service specifications systematically.
Benefits of QFD
- Quality Function Deployment is an effective prioritization method that incorporates many different forms of matrices into one to create a house-like layout.
- Quality Function Deployment is a customer-driven process for planning services and products.
- It begins with the voice of the customer which lays the foundation for the creation of requirements for the products and services.
- Quality Function Deployment helps with documentation and assist in the decision making process.
- QFD assists in translating consumer expectations into clear criteria for products.
- QFD also helps in prioritizing possible product specifications and make trade-off assessments based on weighted consumer expectations and a graded competitive assessment.
Applications of QFD
QFD is used in a wide range of fields, including product design, production, manufacturing, electronics, research and development (R&D), information technology (IT), machinery, software, business and network organizations maintenance, monitoring, regulatory and many other processes.
Some of its other applications are listed below:
- Organizing tasks needed to ensure customer loyalty
- Including strategic strategy
- Manufacturing and distribution
- Sourcing
- Communications
- Sales & operation
QFD is also used for the enhancement of production, quality control, military requirements and consumer goods. And can also be used for customer services applications for improvement in education and hotel services etc.
How Does QFD Work?
The quality function deployment phase begins with the customer (or prospective customers) input compilation usually through surveys. The sample size for such surveys is supposed to be relatively large because quantifiable results would hold greater weight and prevent letting outlier comments drive marketing planning in the wrong direction.
After finishing the surveys and aggregating the data (along with comparative analyzes where applicable the strategy is created based upon the consumer’s voice. These criteria include desires, needs and expectations of consumers.
They are presented as concrete objects and rated preferably in terms of value. These are then listed in the House of Quality matrix on the left-hand side, which shows what consumers expect the product to do.
How To Implement Quality Function Deployment
Let us look briefly at the QFD approach; which can be used to build a process or system that is free from errors. With this methodology, design engineers usually begin progressive drill-down approach with construction planning and go through four steps to get a better understanding of the process management and efficiency required.
In the four-step method, the individual matrix is interconnected to the previous one. The parameters are as follows:
- Product planning QFD - It makes it easier to identify the characteristics of service offerings, which best meet customer requirements, helps to analyze competitive opportunities and also establish critical target values.
- Component Deployment QFD - This helps define the critical sections and assembly components using the functionality of the product prioritized in QFD 1 and determines essential target values.
- Process Planning QFD - helps to identify critical process operational characteristics and features using the components prioritized in QFD 2 and develop critical processing parameters.
- Quality Control QFD - This helps to identify process management processes and conditions and defines systems of development and evaluation that better serve the process of QFD 3 's target process components.
Example of QFD Process
In the diagram depicted below the house of quality, is an important component of QFD, is the fundamental design approach for implementing quality function deployment.
It defines and categorizes consumer preferences, determines the value of those preferences, recognizes technical features that may be important to those preferences, compares the two, allows for clarification of those similarities, and then sets objectives and targets to the device requirements. This method can be applied in the design of a product at any level of system formulation (e.g. system, subsystem, or element) and thus can enable the analysis of possible abstract functions.
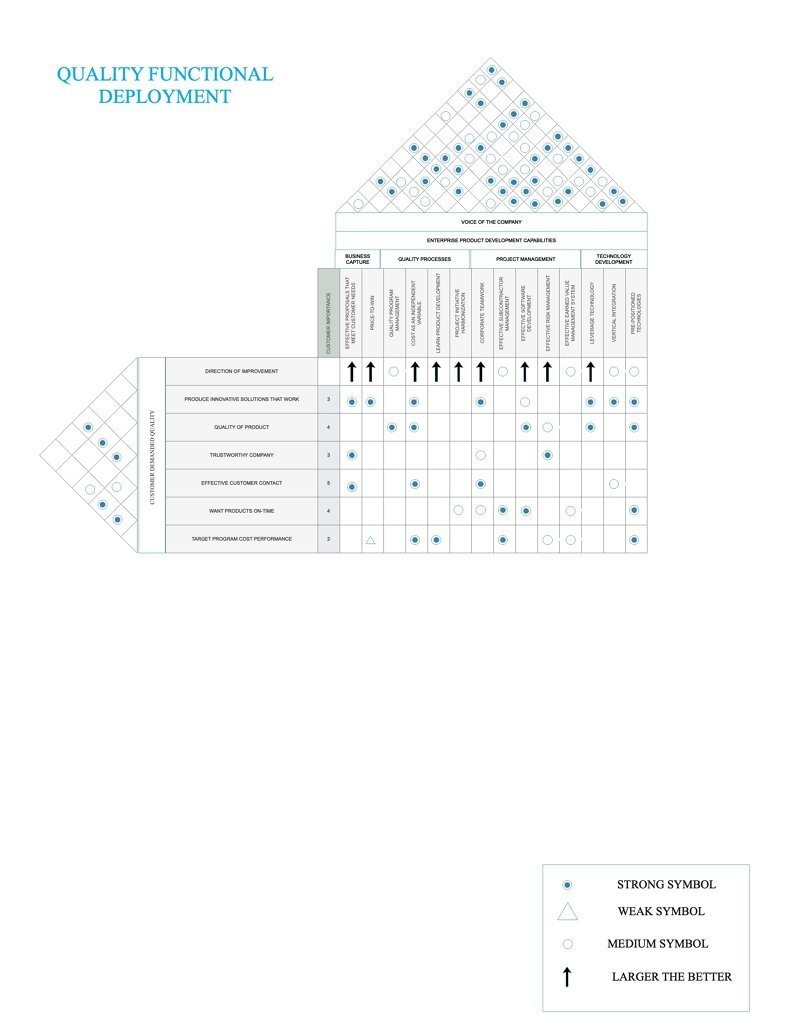
Key Takeaways
Quality function deployment is a framework built to establish quality and incorporate consumer's needs and opinions into a system for better products and services. QFD is better suited as companies rely on comparatively iterative innovation over anything completely new because there is a wide base of consumer feedback and data to guide the process.
Quality function deployment requires more effort to be spent upfront in the production phase so that the team decides, acknowledges and agrees on what needs to be achieved before plummeting into the designing process. As a result, lesser downstream time would be invested in conflicts in opinion on design problems or revision, since the product was not on the schedule. It leads to consensus decision making, increased commitment to the development effort, improved coordination and shortening the time during the operational procedure.