Six Sigma - Methodology, Examples, and Tutorial
Create a Six Sigma Online Free Free Download Free Download Free Download Free DownloadWhat is Six Sigma?
The core of Six Sigma is better understanding of customer requirements and acting on that knowledge by eliminating the issues, defects, and wastes. The underlying processes and systems of statistics, engineering, and project management are put to use to achieve the above objectives.
In statistics, the Greek letter sigma (σ) stands for standard deviation.
There are various definitions of six sigma. Mathematically, the 6 Sigma theory states that it takes six standard deviation events calculated from the mean along a bell curve for an error to occur. Because, probabilistically, only 3.4 out of a million normally distributed random functions (or variables) along a standard curve (or bell curve) falls outside the curve, i.e., six standard deviations or 6σs.
However, in recent years, business management philosophies incorporated Six Sigma as one of its approach towards meeting client requirements.
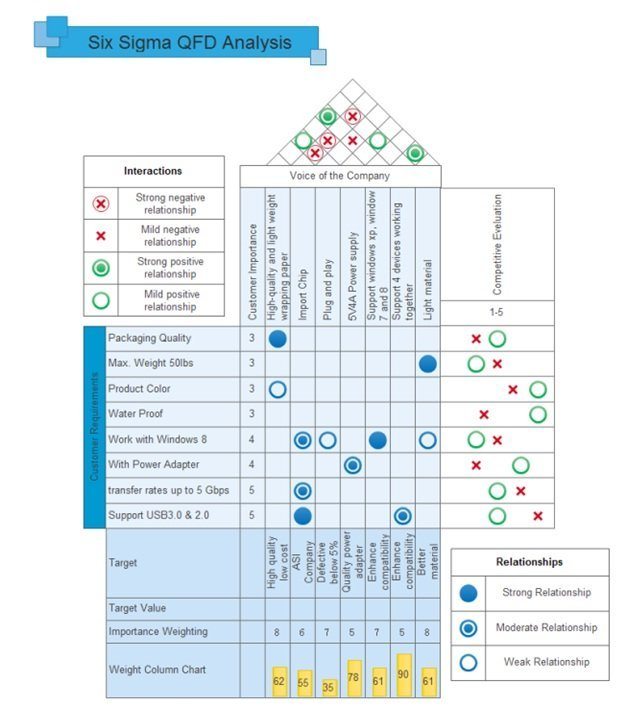
History of Six Sigma
It all started with the introduction of the Normal Distribution and Normal Curve by Carl Friedrich Gauss between the late 1700s and the mid-1800s. However, in 1920, the concept of Six Sigma came up for the first time as a measurement standard for products. It was Walter Shewhart who showed that it takes three standard deviations or σ from the mean is the tipping point where the process needs correction.
Eventually, Bill Smith, an engineer from Motorola Inc., first proposed the term and the concept of Six Sigma in 1986. Subsequently, many businesses and big names incorporated the Six Sigma doctrine. In 1995, General Electric CEO Jack Welch implemented Six Sigma into their operations.
Why do We Use 6 Sigma Methodology?
Process mapping is a process of flowcharting to provide for the documentation of specific business processes. Various ingenious improvement suggestions come out through the flowcharting of work processes.
Waste defined here is anything that is not productive towards the development of services or products delivered to the clients. After identifying the improvement ideas, eliminating wastes is the natural course of action according to the 6 Sigma process.
With quick identification of problem areas and persistent issues, along with effective waste elimination techniques, you can reduce the number of errors substantially. It helps create a satisfying solution for your clients.
If employees get trained in Six Sigma, they have the necessary skill-set to identify the bottlenecks and continuously work to improve the odds. It, in the long run, can improve your services and products significantly.
Six Sigma VS Lean
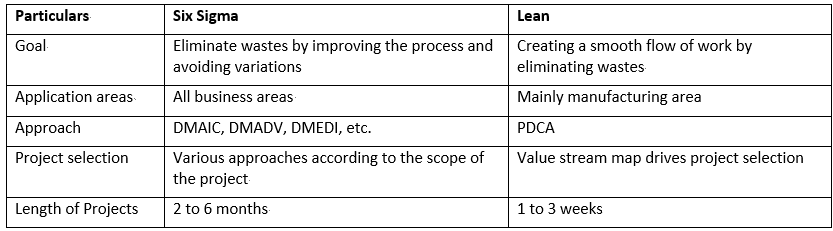
In spite of their differences, both 6 sigma and lean six sigma have the same goal. One can gain several advantages from combining the two.
Nowadays, Six Sigma refers to a combined Lean and Six Sigma methodology for quality-control. The Lean method is for achieving stability, whereas the Six Sigma is for increasing optimization.
Learning the Lean Methodology first gives momentum to solve problems by the Six Sigma Methodology more easily and quickly. Here we will discuss three Six Sigma approaches, DMAIC, DMADV, & LSS.
It is the most basic six sigma approach meaning Define, Measure, Analyze, Improve, and Control. It is a step-by-step process:
- Define: Identify the problems that drive the project, define the methods to be examined.
- Measure: Collect and record data to measure standards, track the effectiveness of the processes, and evaluate their efficiencies.
- Analyze: Identify the types of problems that may arise by reviewing data and utilize critical thinking skills to eliminate them and clarify your goals.
- Improve: Modify your existing business process-planning by testing your solutions to improve them and remove any remaining glitches to align your projects with organization goals.
- Control: Control and sustain these improvements made by monitoring them with a system of control checks.
DMADV is Define, Measure, Analyze, Design, and Verify. It is a complementary approach to DMAIC. While the former focuses on the manufacturing or the product quality, the latter focuses on the customer relations side of a business.
- Define: Identify the customer needs and define your project accordingly.
- Measure: Collect and record data relating to customer needs, product efficiency, product feedback, etc.
- Analyze: Determine the nature of the problem that may arise and act to eliminate it with an alignment with client requirements.
- Design: design your products with the analyzed data to satisfy client needs.
- Verify: Verify the results of your analysis and designing by launching in a live environment and monitor its efficiency.
If we want to talk about LSS or Lean Six Sigma, then we first need to know the Lean methodology developed in Toyota in the 1940s. It is a process similar to 6 sigmas from business perspective made up of the PDCA approach or Plan-Do-Check-Act/Adjust.
Over time both merged to form Lean six sigma. It focuses on the elimination of eight different types of wastes abbreviated as DOWNTIME.
What are Six Sigma Belts?
- Master Black Belt: Train and coach Black Belts & Green Belts and develop metric standards as well as project or workflow direction; functions as six sigma consultant for the company.
- Black Belt: Project leaders, experienced in problem-solving and lead six sigma project teams.
- Green Belt: Assist Black Belts with data collection and analysis.
- Yellow Belt: Project team members tasked with reviewing process improvement.
- White Belt: Freelancers working with the teams but not a part of the organization’s workforce.
- Brown Belt: A Green Belt who has passed the exam for a Black Belt but hasn’t completed any projects since.
How does 6 Sigma work in practice?
In this section, we will look at two real-life examples of DMAIC & LSS application.
Although DEMAIC stands for Define, Measure, Analyze, Improve and Control, sometimes people add an L that stands for Leverage which refers to the applications of the methods learned so far in future related opportunities.
Cleaning your Garage
The best practices are those that start at home. Say you bought a new motorcycle and want to fit it into your garage. Implementing the Lean methods or the DMAIC approach can be optimal for this situation.
- Define: You need to make room in your garage. It means you will have to clean it up; only the garage and not the house, the scope of the project.
- Measure: Identify the quantitative data you need to know, collect, and record them. Here you need to calculate square footage of the garage and the open floor space available. You can set a goal or limit for required open floor space.
- Analyze: Identify and understand what the current types and amounts of materials are and the available storage spaces.
- Improve: Organize your clearing process. You can take the help of 5S and Spaghetti models, remove useless contents, and ultimately install a new storage facility to minimize floor space.
- Control: Label or tag storage spots and conduct weekly audits to ensure no stuff gets accumulated.
- Leverage: With the concept brought into the application phase, you can now use the knowledge from here to manage other tasks of your home.
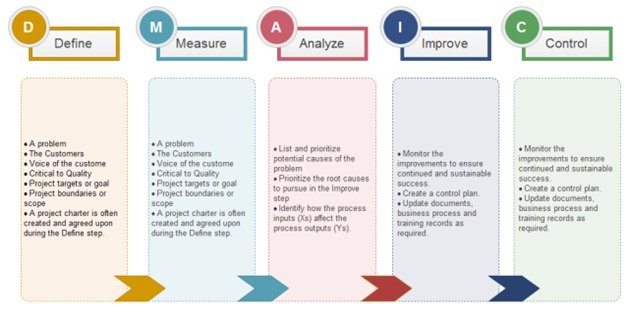
Again like before, I will take an example to understand how six sigma can help in your daily chores, and apply it in your businesses too.
Lose weight using Lean Six Sigma at home
- Define: You need to understand the benefits of the project, set up the timeline of your project, and the team the project will get assigned to.
- Measure:Here, you quantify your problem. Gather all the mathematical and statistical data available on your problem statement and record them to analyze in the next phase.
- Analyze: Consider diet and exercise as the key contributors to weight gain. However, there may be other root causes, like some people are allergic to dairy products, and so on. So, it is crucial to analyze the root causes that contribute to the problem statement.
- Improve: You now need a solution to improve your current state with all the data. You would know what and when you are consuming and how much is your calorie intake in a day.
- Control: This part is very crucial. You may say that I already reached my goal, then why do I need to carry on with the process any longer. Well, if you do not control and sustain your improvement plans, they are most likely to revert to the initial problem state.
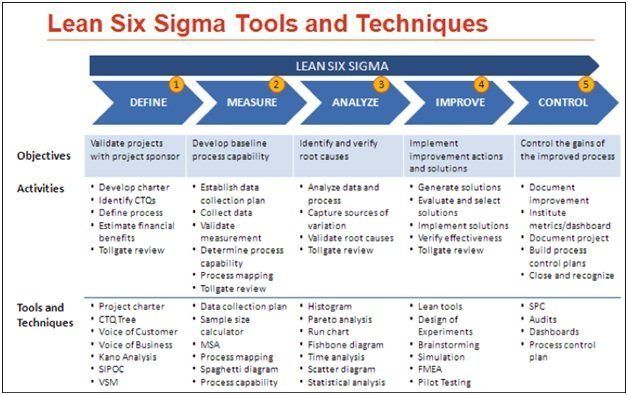
Source: https://www.pinterest.com/pin/450711875190171473/
How to create a Six Sigma Matrix with Edraw?
Edraw’s Six Sigma Matrix tool is beneficial for creating brilliant quality diagram, involvement matrix, prioritization matrix, and feature comparison charts. However, before you create them, there are a few things you need to prepare. You need to know what a Six Sigma Matrix is and the system requirements to run these tools. The Edraw Six Sigma Matrix tool works on Windows 7, 8, 10, XP, Vista and Citrix (for both 32 & 64 bit), Mac OS X 10.2 and later versions. Meanwhile, EdrawMax released the online version, it is worth to try!
- Step 1:Choose the symbols to form the matrix shapes in the library which is to the left of the canvas;
- Step 2:Drag and drop these symbols onto the drawing page;
- Step 3: There is a floating button on the upper right of the canvas that has many options you can use;
- Step 4: You can set the column number, or add/delete a row or a column as per your requirements;
- Step 5: To edit texts in the table, double-click on them and write your own words;
Criticism of Six Sigma
- There are many who believe that employing Six Sigma methodology delays project operations.
- Some say it has nothing new to offer and is merely a marketing tool. However, it still has its unique feature of providing measures like defects per million opportunities, which is a vital metric.
- Others believe that it cannot prevent any mistakes from happening.
- Black Belts and Green Belts get trained, but the remaining workforce has no scope of Six Sigma training leading to human errors in the process.